3D-Druck: Lichtdurchlässige Fassaden mit integrierten Funktionen
Individuelle Gebäudehülle aus dem Drucker
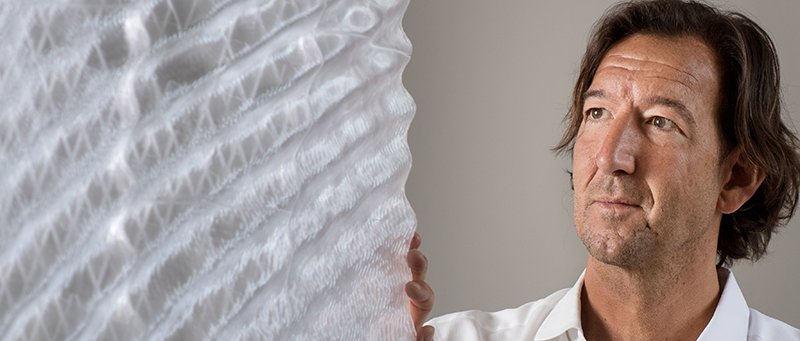
Das 60 Zentimeter breite und einen Meter hohe Muster-Bauteil aus Kunststoff ist schneeweiß und wirkt sehr filigran. Licht scheint diffus durch die Oberfläche. Kaum zu glauben, dass dieses Material ein Gebäude vor Wind und Wetter schützen kann. Bei dem Bauteil handelt es sich um ein funktionsintegriertes Fassadenelement aus dem 3D-Drucker. Moritz Mungenast, wissenschaftlicher Mitarbeiter an der Professur für Entwerfen und Gebäudehülle der TUM hat das Projekt initiiert und es gemeinsam mit seinem Team umgesetzt.
„Tatsächlich ist das Fassadenelement nicht nur sehr stabil, sondern auch lichtdurchlässig und multifunktional“, sagt Mungenast. Zellen im Inneren sorgen beispielsweise für Stabilität und schaffen gleichzeitig luftgefüllte Hohlräume für eine optimale Dämmung. Wölbungen des Materials spenden Schatten. Eingelagerte, dünne Röhren lassen die Luft von einer Seite zur anderen zirkulieren – optimale Belüftung ist damit garantiert. Und eine mikrostrukturierte Oberfläche sorgt für optimale Akustik. All diese Funktionen sind skalierbar und lassen sich ohne extra Kosten individuell an verschiedene Anforderungen anpassen.
Das Geheimnis der Welle
„Der 3D-Druck gibt uns nie dagewesene Gestaltungsmöglichkeiten. Wir können diese Freiheit nutzen, um Funktionen wie Lüftung, Verschattung und Klimatisierung zu integrieren. Das macht teure Sensoren, Steuerungsprogramme und Motoren, die man bisher benötigt, überflüssig“, erklärt der Architekt.
Die Designstudie, die sein Team erstellt hat, zeigt, wie ein Gebäude mit der neuen Lowtech-Fassade aussehen könnte: Kunststoff umhüllt das Bauwerk wie ein luftiges, weiches Tuch. Die Wirkung wird verstärkt durch die gewellte Oberfläche, die dem Fassaden-Konzept seinen Namen gab: Fluid Morphology. Wie Wasserwellen, die entstehen, wenn mehrere Steine in einen windstillen See geworfen werden, überlagern sich die Strukturen: Die Fassade hat große Ausbuchtungen, tritt an einigen Stellen vor, an anderen zurück. Sie ist zudem nicht überall gleich dick – die Variationen erzeugen ein weiteres Wellenmuster.
„Design und Funktion hängen eng zusammen“, erklärt Mungenast. „Wir können beispielsweise die Wellen so anordnen, dass sie die Fassade im Sommer vor Hitze schützten und im Winter möglichst viel Licht durchlassen.“
Langzeittests unter Realbedingungen
Doch wie viel Licht dringt wann und wo durch die neuen, gedruckten Fassaden-Elemente? Wie gut halten sie UV-Strahlung, Windbelastung, Regen und Schnee stand? Wie effizient ist die Dämmung? Eine Langzeitmessung eines kompletten Fassadenelements von 1,6 x 2,8 Metern Größe auf der Solarstation, einem Versuchsstand auf dem Hauptgebäude der TUM in der Münchner Arcisstraße, soll Antworten liefern. Ein Jahr lang werden Sensoren Daten sammeln, mit deren Hilfe die Architekten dann ihr Design noch verbessern wollen, bevor sie einen weiteren Prototyp aus Polycarbonat, einem zugelassenen Fassadenmaterial, fertigen.
Zukünftige Einsatzmöglichkeiten sieht Mungenast zunächst bei Sonderbauten wie Museen, Bibliotheken, Einkaufzentren oder Versammlungsräumen: „Spezielle Lösungen sind hier besonders gefragt, und es spielt keine Rolle, dass die Kunststofffassaden aus dem 3D-Drucker nicht gänzlich transparent sind wie Glasscheiben, sondern transluzent. Das durchscheinende Licht erzeugt eine ganz eigene, durchaus reizvolle Atmosphäre.“
---
Unterstützt werden die Forscher vom Research Lab der Fakultät für Architektur der TUM sowie den 3D-Druckerherstellern Delta Tower sowie Picco’s 3D World.
Bilder und Video zur redaktionellen Verwendung:
Kontakt:
Dipl.-Ing. Moritz Mungenast
Technische Universität München
Professur für Entwerfen und Gebäudehülle
+49.89.289.28486
moritz.mungenast@hk.ar.tum.de
Technische Universität München
Corporate Communications Center
- S. Reiffert
- stefanie.reiffert @tum.de
- presse @tum.de
- Teamwebsite