TUM-Forscher berichten über Arbeit am Gotthard-Basistunnel in der Schweiz
Exakte Navigation und sichere Fahrbahn
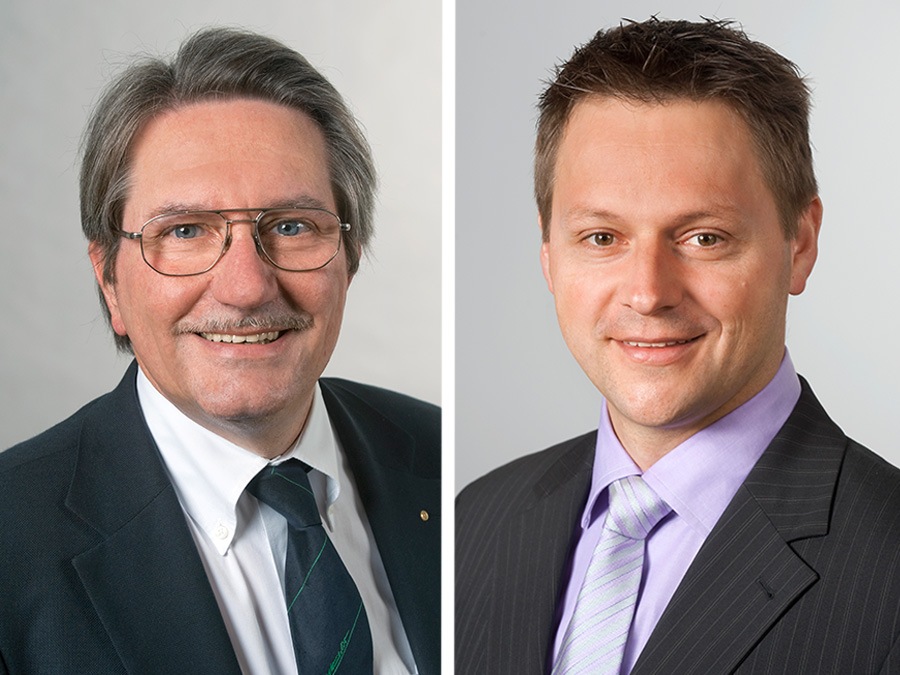
Geodäsie: Zuverlässige Navigation unter Tage
TUM: Herr Prof. Wunderlich, wie war Ihr Lehrstuhl beim Bau involviert?
Wunderlich: Wir haben eine neue Messmethode entwickelt, die eine exakte Orientierung am Boden eines Schachtes erlaubt. Gebaut wird ein Tunnel mithilfe riesiger Tunnelbohrmaschinen oder durch Sprengungen und Bagger, Fachleute sprechen dabei vom Vortrieb des Tunnels. Die zentrale Kompetenz eines Ingenieurgeodäten ist es dabei sicherzustellen, dass zwei gegenläufige Vortriebe, die von verschiedenen Stellen beginnen, sich auch nach Kilometern auf wenige Zentimeter genau treffen. Insbesondere, wenn es sich um einen Eisenbahntunnel für Hochgeschwindigkeitszüge handelt, ist eine extrem hohe Genauigkeit nötig. Gibt es auch nur eine Abweichung von einigen Dezimetern, können die Gleise nicht mehr so verlegt werden wie geplant. Das hätte zur Folge, dass die Züge wesentlich langsamer fahren müssen.
TUM: Wie viele Vortriebe gab es beim Bau des Tunnels?
Wunderlich: Würde der Tunnel nur von den beiden Endpunkten aus gebohrt, wäre man noch lange nicht fertig. Daher gibt es zwei zusätzliche horizontale Zugänge zur geplanten Tunnelachse. Es werden dabei künstliche Hohlräume geschaffen, von denen aus dann nach zwei Seiten vorgetrieben werden kann. So können viele Maschinen gleichzeitig kürzere Strecken bohren. Die Geodäten haben dabei die Aufgabe, die Maschinen zuverlässig zu navigieren. Die Herausforderung am Gotthard-Basistunnel war, dass es einen vertikalen Zugang in Sedrun durch einen Schacht von 800 Metern Tiefe gab. Stellen Sie sich die Frauenkirche achtmal übereinander vor, das ist schon enorm. Das Problem dabei ist nun: Wie kann man die geometrischen Referenzpunkte an der Oberfläche mit genügend Genauigkeit nach unten übertragen, um der Maschine den Weg zu weisen?
TUM: Wie haben Sie das Problem gelöst?
Wunderlich: Mit GPS-Satelliten kann man Referenz-Koordinaten oberhalb des Tunnels festlegen. Die Übertragung der Koordinaten in die Tiefe kann mithilfe von mechanischer und optischer Lotung stattfinden. Das haben die Schweizer exzellent gelöst. Die zweite Aufgabe war die Anfangsorientierung der Vortriebe vom Schachtboden aus. Zur Richtungsbestimmung werden normalerweise Vermessungskreisel genutzt, die auch unter den besonderen Bedingungen im Tunnel den Bezug zur Nordrichtung herstellen können. Wenn die Temperatur in der Tiefe allerdings 40 Grad überschreitet, sind die Geräte aber außerhalb ihres Eichbereiches und werden ein wenig ungenauer. In der Kooperation mit der ETH Zürich haben wir deshalb eine unabhängige neue Methode entwickelt.
TUM: Nach welchem Prinzip funktioniert die Methode?
Wunderlich: In dem Förderkorb, der für den Materialtransport durch den Schacht genutzt wird, haben wir eine spezielle Sensorik angebracht, das sogenannte Inertialmesssystem. Mit dieser Plattform können wir messen, wieweit sich der Förderkorb verdreht, wenn er von oben nach unten fährt. Zunächst überträgt ein Geodät die Orientierung des obertägigen Netzes, das wir durch GPS erhalten haben, auf ein spezielles Spiegelsystem auf der Plattform. Jetzt fährt der Korb nach unten. Unten übertragen wir die Orientierung mit derselben Methode auf das untertägige Netz. Die Korrekturgröße von oben nach unten ist der von der Trägheitsplattform gemessene Verdrehungswinkel.
TUM: Gab es noch andere Herausforderungen bei der Arbeit am Gotthard-Basistunnel?
Wunderlich: Der gesamte wissenschaftliche Aufwand war eigentlich vertretbar gegenüber dem logistischen Aufwand, der nötig war, damit wir einen Tag für acht Stunden den Förderkorb für die Messungen im Schacht benutzen konnten. Der Schacht war ja sozusagen die Aorta, und wenn er von den Geodäten für einen Tag blockiert wird, musste das ein Jahr vorher penibel geplant werden. Das heißt aber auch, es musste unbedingt funktionieren. Dazu haben wir tagelang am Betriebsaufzug im Olympiaturm in München trainiert, damit alles reibungslos läuft.
Verkehrswegebau: Die beste Materialkomposition für die Feste Fahrbahn
TUM: Herr Prof. Freudenstein, Sie waren mit Ihrem Lehrstuhl und Prüfamt für Verkehrswegebau am Gotthard-Basistunnel beteiligt ...
Freudenstein: Ja, wir haben wesentlich an der Gestaltung des Eisenbahnoberbaus mitgewirkt. Im Gotthard-Basistunnel liegen die Schienen und Schwellen nicht im Schotter, sondern es wurde eine Feste Fahrbahn hergestellt. Es kam das für die Schweiz typische Feste-Fahrbahn-System LVT zur Anwendung. Dabei werden Betonblöcke, die in einem Gummischuh elastisch gelagert sind, in den umgebenden Tragplattenbeton eingegossen. Da sich mehr als zwei Kilometer Gestein über dem Tunnel befinden, ist die Temperatur aus dem Gesteinsdruck dort sehr hoch. Es ist im Tunnelinneren bis zu 40 Grad heiß. Diese Temperaturen wirken sich auf die Fahrbahn aus. Elastische Komponenten einer Festen Fahrbahn verhalten sich bei höheren Temperaturen anders.
TUM: Wie haben Sie diese Veränderungen untersucht?
Freudenstein: Wir haben einen Teil der Fahrbahn in unserer Prüfhalle aufgebaut und auch die klimatischen Bedingungen nachgestellt. Dann haben wir geprüft, ob die Elastizität auch nach millionenfacher Beanspruchung durch die pulsierenden Achsüberfahrten noch vorhanden ist. Wir haben verschiedene Materialkompositionen untersucht, um die beste Zusammensetzung zu finden. Vor einigen Monaten waren wir auch bei den sogenannten Hochtastfahrten vor Ort, um das Einsenkungsverhalten des Gleises unter dynamischer Belastung zu verifizieren. An mehreren Querschnitten im Tunnelinneren haben wir unsere Messtechnik eingebaut und von außen über eine von uns entwickelte Datenfernübertragung gesteuert. Dabei hat ein deutscher ICE die Hochtastfahrten mit Geschwindigkeiten von bis zu 275 Stundenkilometern absolviert.
TUM: Was war das Besondere bei der Arbeit im Gotthard-Tunnel?
Freudenstein: Der Arbeitsweg ist ungewöhnlich. Der Tunnel hat eine Länge von etwa 57 Kilometern. Man fährt also von einer Seite im Mittel bis zu 28,5 Kilometer weit hinein zur seiner Arbeitsstelle. Mit 40 Kilometern pro Stunde dauert es bis zu einer Stunde, bis man an dort angekommen ist. Die Arbeit selbst ist aber sehr sicher, jeder muss beispielsweise einen Rucksack tragen, der registriert ist, und man kann immer geortet werden.
Weitere Informationen:
Technische Universität München
Corporate Communications Center
- Stefanie Reiffert
- reiffert @zv.tum.de
- presse @tum.de
- Teamwebsite