Classification system for robot fitness
TUM creates seal of approval for robotics
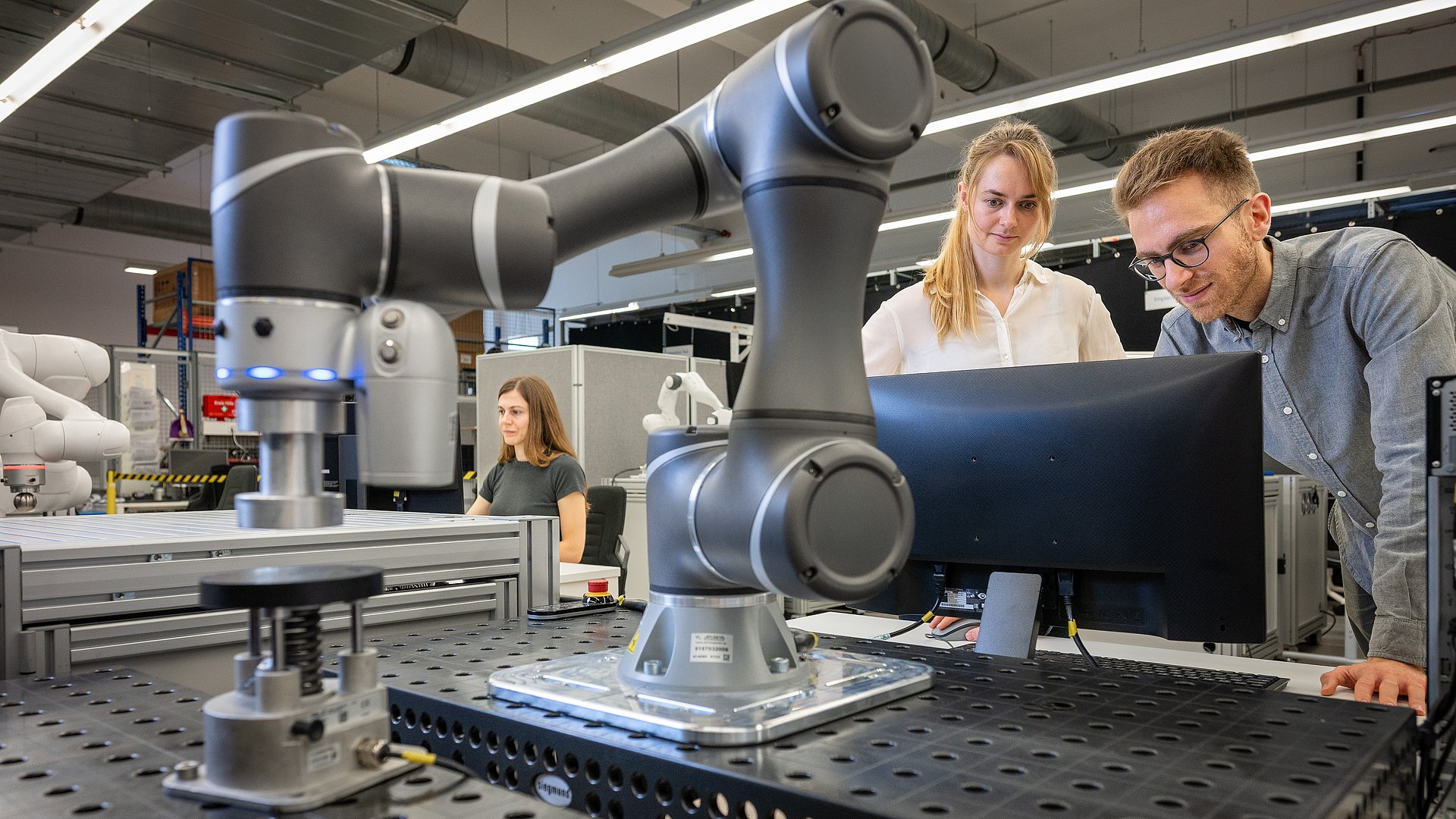
Achim Lilienthal, Deputy Director of MIRMI and Professor of Intelligent Systems Perception, is convinced: “The TUM MIRMI test methodology has the potential to become an industrial testing standard.” This would create the conditions for establishing a seal of quality for the fast-growing robotics market. “Knowing the performance capabilities of a robot system is an enormous help to industry, where companies want to make the best possible use of robotic systems.” TUM MIRMI Executive Director Prof. Lorenzo Masia says: “Based on the original idea, I am certain that the AI Robot Safety & Performance Centre at TUM MIRMI will develop into an independent national testing center for robotics.”
Single-armed robots as a starting point
As a first step, the researchers examined and categorized single-armed robots from well-known manufacturers that are used in industry and research. Although many robotic arms look similar, they each have their own strengths and weaknesses, with big differences between sensors, motors and the actual brain of the intelligent machines. This results in systems that differ greatly in their basic capabilities. Some are powerful and precise in their movements, while others are gentle, flexible and sensitive in their interaction with their surroundings.
To highlight these differences and the continuous progress of robotics, researchers at TUM MIRMI's AI Robot Safety & Performance Centre have developed the Tree of Robots. Based on Charles Darwin's Tree of Life, it depicts the fundamentally different adaptations of various species to their ‘habitat’, in this case not of living beings, but robots. “To do this, we look at the basic skills a robot needs in processes, such as how well it follows a given path, takes up a position, how gently it can make contact with surfaces, and how safe it is in dealing with collisions between robots and humans,” explains lab director Robin Kirschner.
25 measurements of robot sensitivity
For tactility alone, there are 25 measurements that describe a robot’s sensitivity in physical contact with its surroundings. Among other things, this involves finding out whether the force applied to a surface, for example, is not actually higher than intended or whether a robot could cause injury to humans. From the pattern that emerges on a spider diagram based on the 25 measurements, even laypeople can see the robot’s sensitivity at a glance.
A clear picture of a robotic system’s strengths and weaknesses
Based on the performance of individual systems, researchers categorize them as ‘industrial robots,’ ‘cobots,’ ‘soft robots’ and ‘tactile robots.’ For surgical robots the decisive requirement is precision. For warehouse or factory applications, by contrast, the emphasis is on strength and resilience, i.e. the ability to perform repetitive movements over long periods. “We combine existing motion metrics with our new tactile metrics to provide the first-ever overview of the totality of the basic capabilities for physical interactions of a robotic system,” explains Kirschner.
blablabla
Robin Jeanne Kirschner, Kübra Karacan, Alessandro Melone and Sami Haddadin; Categorizing robots by performance fitness into the tree of robots; Nature Machine Intelligence, 24.3.2025; https://www.nature.com/articles/s42256-025-00995-y
The Munich Institute of Robotics and Machine Intelligence (TUM MIRMI) is an integrative research institute at the Technical University of Munich, where researchers develop intelligent machines that interact with humans and are capable of learning. More than 70 professors from TUM are involved in TUM MIRMI, focusing on robotics applications, perception and artificial intelligence. The focus is on applications in the fields of health, work, environment and mobility. A five-member Board of Directors defines the research and innovation strategy as well as the core teaching content of TUM MIRMI, establishes and coordinates new focus groups, appoints new research and innovation leaders, and proposes new members for the Science Advisory Board and the Industry Advisory Board. The Board of Directors consists of Prof. Lorenzo Masia (Executive Director), Prof. Achim Lilienthal (Deputy Director and Director of Strategy and Partnerships), Prof. Angela Schoellig (Director of Industry and International Affairs) and Prof. Eckehard Steinbach (Director of Start-ups and Infrastructure). More information: https://www.mirmi.tum.de/mirmi/startseite/
Technical University of Munich
Corporate Communications Center
- Andreas Schmitz
- presse @tum.de
- Teamwebsite
Contacts to this article:
Robin Kirschner
Laboratory Manager, AI Robot Safety & Performance Centre
Munich Institute of Robotics and Machine Intelligence (MIRMI)
Technical University of Munich (TUM)
robin.kirschner @tum.de
Prof. Achim Lilienthal
Chair for Perception for Intelligent Systems
Technical University of Munich (TUM)
achim.j.lilienthal @tum.de